Industrial bucket moulds are essential tools in revolutionizing the production line of bucket manufacturing. By embracing the efficiency they offer, manufacturers can streamline their operations and achieve several benefits. Increased Productivity: Industrial bucket moulds are designed to optimize the production process, enabling manufacturers to produce buckets at a faster rate. With the use of advanced manufacturing techniques, such as multi-cavity moulds or high-speed injection moulding, multiple buckets can be produced simultaneously, reducing cycle times and increasing overall productivity. Consistent Quality: Industrial bucket moulds ensure consistent quality in each produced bucket. The moulds are precisely engineered to maintain uniformity in shape, size, and structural integrity of the buckets. This eliminates variations and defects that may occur with manual or less precise production methods, ensuring that every bucket meets the required standards. Cost Efficiency: The efficiency of industrial bucket moulds can result in significant cost savings for manufacturers. With faster production cycles and reduced labor requirements, manufacturers can save on labor costs. Moreover, the consistent quality and reduced waste associated with well-designed moulds minimize material waste and rework, leading to cost reductions in raw materials. Design Flexibility: Industrial bucket moulds offer design flexibility, allowing manufacturers to produce buckets with various shapes, sizes, and features. moulds can be customized to accommodate specific design requirements, such as handles, spouts, or logos, providing a range of options for different applications. This flexibility enables manufacturers to cater to diverse customer needs and expand their product offerings. Longer mould Lifespan: Industrial bucket moulds are typically made from durable materials, such as steel or aluminum, which can withstand the rigors of high-volume production. These moulds are designed for longevity and can withstand repeated use without significant wear or degradation. This results in a longer mould lifespan, reducing the need for frequent mould replacements and associated costs. Streamlined Workflow: Integrating industrial bucket moulds into the production line streamlines the workflow and reduces production bottlenecks. The moulds can be seamlessly integrated with automated systems, such as robotic arms or conveyors, to facilitate efficient material handling and mould changing processes. This optimizes the overall production flow and minimizes downtime, enhancing operational efficiency. Scalability and Volume Production: Industrial bucket moulds are scalable, allowing manufacturers to scale up production according to demand. As the moulds can accommodate multiple cavities, manufacturers can produce a higher volume of buckets in a single production cycle. This scalability is particularly beneficial for industries with fluctuating demand or seasonal variations. Quality Control and Traceability: Industrial bucket moulds facilitate quality control and traceability throughout the production process. By implementing quality control measures and monitoring parameters, manufacturers can ensure that each bucket meets the required standards. Additionally, moulds can be marked or coded for traceability, enabling better control and tracking of production batches.
In summary, industrial bucket moulds revolutionize the production line by increasing productivity, ensuring consistent quality, reducing costs, offering design flexibility, prolonging
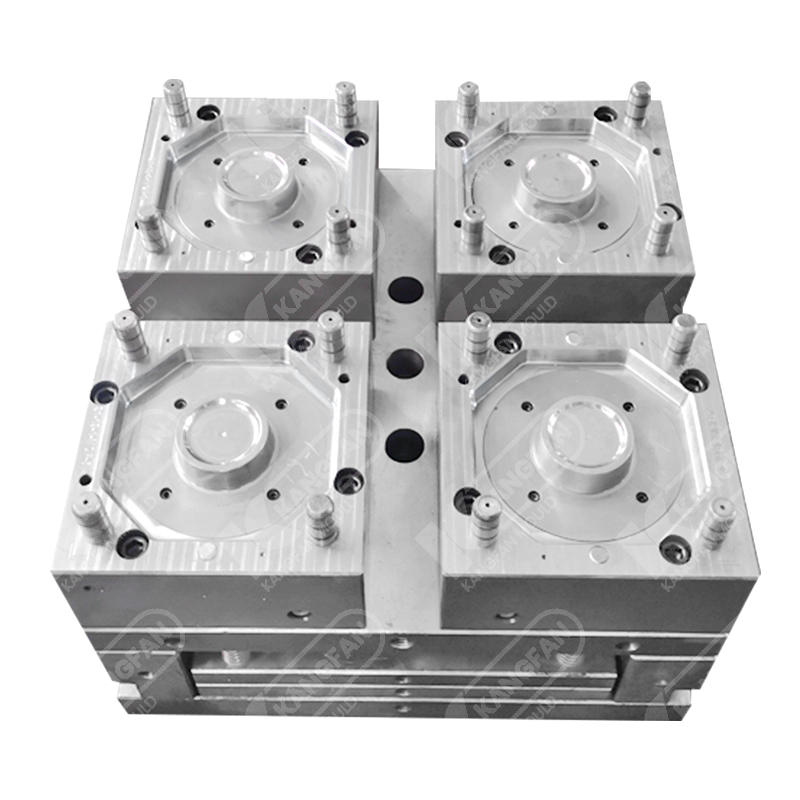